26.06.17 – DITF
Digitale Mikrotextilfabrik
So geht Textilproduktion heute und in Zukunft – die Messe Texprocess 2017 präsentierte live eine digital integrierte Produktionskette für Bekleidung.
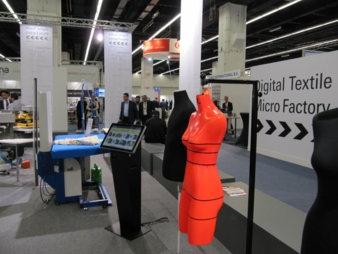
Digitale Technologien haben das Potenzial, einen Paradigmenwechsel einzuleiten und bieten Unternehmen völlig neue Chancen. In diesem Zusammenhang und in Zusammenarbeit mit renommierten Partnern präsentierten die Deutschen Institute für Textil- und Faserforschung Denkendorf (DITF) die „Digital Textile Micro Factory“ auf der diesjährigen Texprocess 2017 © Iris Schlomski
Die diesjährigen Besucher der Texprocess konnten eine vollständig vernetzte und integrierte Fabrik erkunden: angefangen beim Entwurf, Gradierung, Schnittlagenbild über den Digitaldruck bis zum automatisierten Einzellagenzuschnitt und von da aus direkt in die Konfektion und zum Finish.
Die nahtlose digitale Vernetzung der Produktionsschritte innerhalb der Micro Factory haben den weiteren Vorteil eines optimierten Materialverbrauchs bei gleichzeitig kürzeren Bearbeitungszeiten für Aufträge bei gleichzeitigem Höchstmaß an Flexibilität.
„Mit der Digital Textile Micro Factory können Teile der Textilproduktion zurück nach Europa geholt werden“, ist sich Christian Kaiser, Projektmanager an den DITF sicher. Die vernetzte Produktion sowie das digital durchgängige Engineering ermögliche wettbewerbsfähige und lokale Produktion individualisierter Produkte. Für Professorin Meike Tilebein, Leiterin des Bereichs Management Research an den DITF ist die Digital Textile Micro Factory mit 3D-Design, vernetzte Produktion und modernste Technologien sogar „ein Meilenstein auf dem Weg zu Fast Fashion”.
Neue Technologien und integrierte Workflows geben der Textil- und Bekleidungsindustrie ein neues Gesicht
In der ersten Stufe der Micro Factory wurde innovative 3D-Simulations- und CAD Technologie eingesetzt. Mithilfe von CAD (computergestütztes Design) und der 3D-Simulationssoftware Vidya wurden kreative Designs digital in Szene gesetzt. Die 3D-Simulationsdaten wurden darüber hinaus mit den Daten für die nachfolgenden Prozesse zusammengeführt, zum Beispiel für den digitalen Textildruck, den automatisierten Einzellagenzuschnitt und die Konfektion. Partner im Bereich Design war Assyst, ein Unternehmen der Human Solutions Group. Printcubator von Mitwill steuerte individualisierte Designs als Grundlage für den 3D-Design-Prozess bei.
Textildruck
Die nächste Stufe zeigte großformatigen Tintenstrahldruck, unter Anwendung von Sublimationsdruckverfahren auf Polyester sowie Pigmentdruck auf Baumwoll- und Mischfasern. Produktionsaufträge konnten auf diese Weise flexibel mit unterschiedlichen Druckparametern kombiniert werden. Die Farbgenauigkeit wurde durch die Nutzung der Multispektraltechnologie garantiert, womit auch eine farbverbindliche Rekolorierung von Stoffproben möglich ist. Partner im Bereich Soft- und Hardware waren Caddon Printing and Imaging, Ergosoft und Mimaki sowie Coldenhove und Monti Antonio, die für die optimalen Druckergebnisse an dieser Station sorgten. Polyesterstoffe der Premiumklasse für sportliche Anwendungen wurden von Eschler Textil und Schoeller Textil zur Verfügung gestellt.
Zuschnitt
Im Zuschnittbereich wurden die individuellen Aufträge völlig automatisch mit Hilfe eines QR-Codes von einer Kamera identifiziert. Diese Erkennung ermöglicht ein automatisches Laden der zugehörigen Zuschnittdateien und eine kontextspezifische Anpassung des Zuschnitts. Der Abroller des Einzellagentisches stellte sicher, dass das Material so glatt wie möglich und ohne Verzug transportiert wurde. Durch Kamerasysteme wurden auch Positionsmarker identifiziert, wodurch die Schnittpfade nochmals optimiert und ein erstklassiger Zuschnitt erreicht wurde. Partner in diesem Bereich war die Firma Zünd.
Konfektion
Der Bereich Konfektion zeigte den Prozess der programmgesteuerten Einrichtung. Hier wurden die Zuschnitte der verschiedenen Aufträge zum endgültigen Kleidungsstück genäht oder verschweißt. Dies erfolgte auf modernsten Nähmaschinen, die auch für den vernetzen Einsatz geeignet sind. Weiterhin war in diesem Bereich die neueste Ultraschall-Schweißtechnologie für Bekleidungsstoffe zu bestaunen. Partner in diesem Bereich waren Dürkopp Adler und Pfaff. Die Garne wurden von Coats Thread Germany zur Verfügung gestellt.
Finish
Im Bereich Ausrüstungstechnologie und Dampferzeugung sahen die Besucher innovative und energieeffiziente Geräte. Partner in diesem Bereich war Veit. In diesem Schritt wurden die Bekleidungsstücke vom Partner Seripress auch mit waschbaren Logos etikettiert und grafischen Details ausgestattet.